Mould flow analysis predicts a lot about the process of injection moulding plastic products
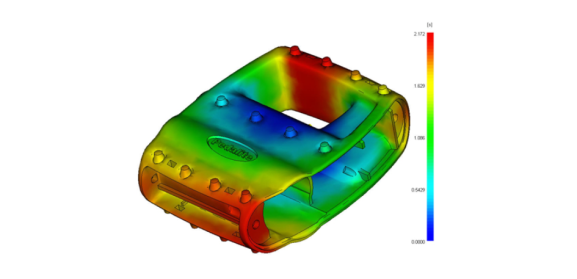
During a mould flow analysis, it is digitally simulated how a mould will function and how this can be optimized by adjusting the various variables. And that even before the mould has actually been made! In this way, the injection moulding process can be accurately adjusted before it has even started.
In-house mould flow analysis perfects the injection moulding process before it has begun
In injection moulding, many variables influence the final shape and possibly also the functioning of the product. For example, the temperature of the plastic during injection moulding and the way it cools and hardens, possible warpage (product deformation), the point of injection or the forming of flow lines. Mould flow analysis shows how a mould will function and how this can be optimised by adjusting various variables. And that’s even before the mould is actually made! In this way, the injection moulding process can be fine-tuned even before it has even begun.
A mould design is based on the desired plastic product’s 3D drawings. Nevertheless, there are always uncertainties (although sometimes minor, they are no less important) concerning the final functioning of the mould, as every product and every mould are different. A mould flow analysis literally shows how the (liquid) plastic will flow into the mould and how the plastic will then cool and ‘harden’.
What variables?
The injection moulding process is influenced by several factors. They all have their own consequences.
Temperature affecting the flow of plastic
.
.
The different stages of introducing plastic into a mould.
The colour indicates the temperature of the liquid plastic: red is hot and blue is
cool(er). The further the plastic enters the mould, the more it cools down.
.
Materials, including plastic, expand when heated and shrink when cooled. This expansion and contraction can seriously impact the appearance and functioning of the plastic product. For example, because parts of a plastic product do not always have the same thickness ('wall thickness'), a (thinner) part can cool down faster than another (thicker) part, which causes tension in the product and possibly warping when it is removed from the mould. The shape of the mould (and therefore the product) can also cause different degrees of pressure in different places in the mould. This may deform the product. This deformation is also referred to as 'warpage'.
.
Mould flow analysis shows where possible warpage will occur
If the mould flow analysis shows that warpage will occur, this can be counteracted in various ways, for example, by adjusting the production process and allowing the product to cool down in the mould more slowly. However, this means that the cycle time (the time needed to make the product) will be longer and therefore more expensive. Cooling the mould locally during injection moulding or modifying the product or mould design may also be possible.
Injection points: place and temperature are also important
The way the molten plastic flows into the mould is influenced by the number of injection points and their placement. Optimum flow of the plastic can be achieved by adjusting this during the mould flow analysis. The functioning of any hot runners can also be analysed. These ensure the direct and heated injection of the liquid into the mould’s cavity without requiring injection channels inside the mould where plastic can collect and harden.
When designing a mould, careful consideration is given to the placement and function of the injection points - the points where the liquid plastic is injected into the mould.
.
‘Bubbles’ due to trapped air
The mould cavity may not be completely filled if the molten plastic does not flow as desired: some air may become trapped in the mould and therefore the product. This is generally undesirable, as bubbles can weaken that spot in the product. Air bubbles on the surface of the product are also ugly. Finally, residual air in the mould can also cause burns in the product. Mould flow analysis helps to predict if and where air could get trapped in the mould, so this can be prevented by modifying the mould or product.
One machine is not the other: clamping force and holding pressure
As already mentioned, every product and every mould are different. To fill a mould with plastic, the two parts of the mould must first be clamped together in such a way that no molten plastic can leak out of the mould’s cavity. After all, the plastic is injected into the mould under high pressure (the clamping force of the machine is indicated in tonnage). This pressure causes the plastic to liquefy. The greater the clamping force required, the stronger the injection moulding machine must be. And the stronger the machine, the more expensive the production on that machine is.
As soon as the molten plastic flows into the mould, the plastic begins to cool down and harden, and it may also shrink. To ensure that the molten plastic reaches all the corners and details of the mould, the machine increases the pressure during injection. This is referred to as ‘holding pressure’.
Mould flow analysis can be used to fine-tune the process to find an optimal balance between (machine) costs and the required clamping force or holding pressure.
Flow seams where two streams of liquid meet
Multiple streams of liquid enter a mould at the same time when multiple injection points are used. These flows generally meet up with each other somewhere in the mould; at that point, a so-called flow seam or flow line forms. A weak(er) spot can form at such a flow point in the product depending on, for example, the temperature of the various plastic flows.
In addition, a flow seam may be visible, which is often undesirable. A mould flow analysis will detail where flow seams will arise. Whether the flow seam is acceptable or whether a change to the product, mould or process is necessary can be decided in consultation with the customer.
Working method
All of the above factors influence an injection moulding process. A mould flow analysis provides very detailed predictions on the course of that process. Our engineers will be happy to advise you on whether such a detailed analysis would add value to your new product.
If the customer decides to have a mould flow analysis performed, modifications to the product, mould or process will be subsequently proposed to the customer on the basis of the findings. After such an iteration (modification), a new mould flow analysis may be performed to assess the results.
Pekago has the technology to perform a mould flow analysis in-house. For more information, please contact our engineers.