Spuitgieten, TSG, lakken en assembleren van uw kunststof behuizingen en technische componenten
"Plastics are essential for achieving the CO2 targets for the aerospace industry"
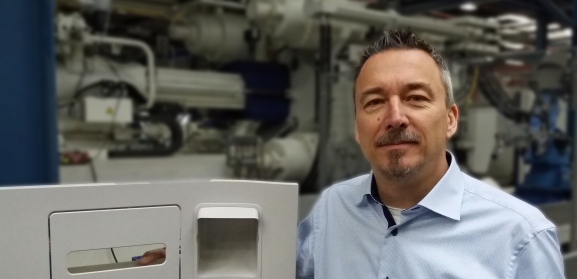
“I dare to say that plastics will be increasingly used in the aerospace industry in the future. Plastics have important properties that traditional aircraft materials, such as aluminium, cannot compete with”. Speaking was Hermann Thorsen, our key account manager for Aircraft Interiors. In this blog, he speaks about the applications of plastics in the aircraft industry.
"Moreover, many plastics are lighter in weight. A lighter aircraft needs less fuel, which is a huge advantage in these times when energy consumption is under scrutiny. Other trends in the aviation industry have also contributed to the increased use of plastics”. Speaking was Hermann Thorsen, our key account manager for Aircraft Interiors. Hermann has been taking care of Pekago's aerospace customers since 2010 and is well versed in the international market.
Airbus now also has aircrafts with a similar internal |
. |
Interior components and vital components:
different plastics
“Plastic is now widely used for so-called interior components, i.e. injection-moulded components that are visible to passengers in the aircraft. Plastic components are also found behind the walls: These are generally technical injection-moulded components, such as brackets and climate control components. Composite is usually used for the so-called 'vital' parts of the aircraft, a material that Pekago does not use, that is the expertise of other companies. For the injection moulding of aircraft interior components, high performance plastics, such as PEI, PEEK, PC and PPS, are generally used”.
High-performance materials
Hermann continued enthusiastically: “These high-performance plastics meet the high requirements that aviation places on materials in the field of, for example, FST (Fire, Smoke and Toxicity). Aircraft - and therefore also the plastic components used in them - must be as fire-resistant as possible and must not or must only emit as little as possible toxic fumes or smoke under extreme conditions, as the emission of toxic fumes and smoke would be catastrophic. The online IAQG OASIS database must always be consulted before an aircraft manufacturer engages a certain supplier/manufacturer. This database contains a list of certified companies that meet the requirements of aviation. As a supplier, ISO9001 certification is really not enough; the aviation industry demands the much more extensive AS9100”.
“Special requirements are placed on the finishing of injection-moulded components intended for the aerospace industry. If injection-moulded components must be painted, the paint must also meet these requirements. The aerospace industry is making ever increasing demands. For example, water-based paint is another requirement for all interior components. The high requirements in the aviation industry have increased the demand for high-performance plastics and special water-based paints.
A mould for injection moulding
of the plastic coating of a
toilet unit in an Airbus A330 NEO
Experience
“The vast majority of interior components are actually painted after injection moulding. This contributes to the functionality of the product, but also to producing a beautiful and luxurious appearance, which is in its turn important for the passenger experience. The trend in aviation is that aircraft models are less frequently replaced. But flying to your destination in an 'outdated' aircraft gives no one a good feeling. That's why aircraft are increasingly 'refurbished', an interior makeover, with new fresh interior parts, sometimes even in bright colours!” said Hermann with a wink. “Refurbishing aircraft offers opportunities to plastic injection moulding companies. But margins are under pressure, so know-how, efficiency and first-time-right are more important than ever. Consequence: high demands are placed on suppliers”.
Aviation, environment and growth
“It will not have escaped anyone's attention that the environmental aspects of aviation are being looked at very critically”, Hermann continued. “Under public opinion’s critical eye, the aviation industry has set itself the target of reducing CO2 emissions to half the 2005-level by 2050. 2050 is a long way off, but this is a very ambitious goal, especially since the prediction is that aviation will grow rapidly in the decades to come. This applies to the number of kilometres flown, the number of passengers and the number of aircraft. Boeing and Airbus each expect to sell some 35,000 aircraft by 2036. So this ambitious target for CO2 emissions offers great opportunities for manufacturers of injection-moulded components for applications requiring components made of light plastics”.
. . By the way, did you know that plastic components . . |
. |